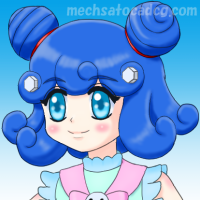
今回は3DCADを使用した設計方法について解説します。
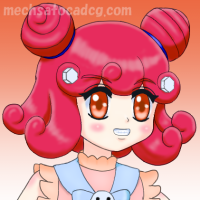
そんなの部品を一個ずつモデリングして、最後に部品を全てアセンブリに入れて、合致をかけるだけでしょ?
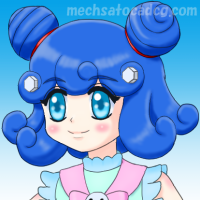
手描きや2DCADで、設計が終わっているものであれば、その流れでモデルを作成すればいいと思うけど、今回は全くゼロの状態から設計する場合についてなの。
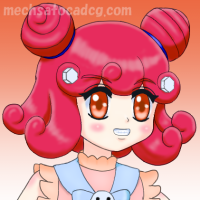
そんなこと、出来るの?やれんの?
吐いた唾は飲み込めないんよ!
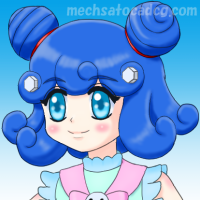
(……漫画かプロレスの影響かな?)
出来るから、以下の解説を読んでみてくださいね。
すでに3DCADは設計ツールとして、企業に浸透しておりますが、3DCADを使ってゼロから設計をするのは、2DCADや手描きで設計するのとは勝手が違います。
製造工程の前倒し(フロントローディング)のために、高いCAEツールやCAMと共に3DCADを導入したのに、なかなか設計が進まず、結局2DCADで設計し、後にCADオペレータに3D化して貰っていたのでは本末転倒です。
筆者も、3DCADを覚えたての頃に、カバーの設計を任されたことがありますが、なかなか進まず深夜残業、休日出勤が続いたことがあります。
結局、誰にも教えられることなく、2、3年かけて自分で勉強をして覚えていきました(苦笑)
結論から申しますと、3DCADで設計を行う上で最良の方法とは、構想図から必要部品をリストアップし、部品を1フィーチャだけ作りアセンブリに投入、各パーツモデルを並行に、重要部分から作り上げて、アセンブリ上に配置をしていくことです。
決して、部品を一品一品作りこんでから、アセンブリに入れてゆくのでは無いということです。
以下で、詳細を説明していきたいと思います。
CADはAutodesk Fusion(旧Fusion360)を使用しております。
【広告】
ものづくりのプロジェクト計画、設計、運用、構築ツールをお探しの方はこちら
3D・CGモデリングのスキルを持った方々をお探しの方はこのテキストリンクから


3DCADで設計を行う際の前準備
まずは3DCADで設計を行う前準備です。
手順としては、
- 構想図(ポンチ絵)の作成
- パーツのリスト
これらが必要となります。
構想図
構想図に関しては、手描きや2DCADで設計する際に描くものと同じものです。
次で説明する、パーツのリストが作れるくらい、形状が分かるものであれば十分だと思います。
パーツのリスト
パーツのリストは、構想図から、その機械を構成する部品を書き出したものです。
構想図から「ベース」「ピン」「シャフト」「ギア」と抜け、重複が無いように、チェックをしながら、レポート用紙や紙に書き出していきます。
また、この時点で同じ機構や機能、可動する部品群を、サブアセンブリ化することも検討しておきます。
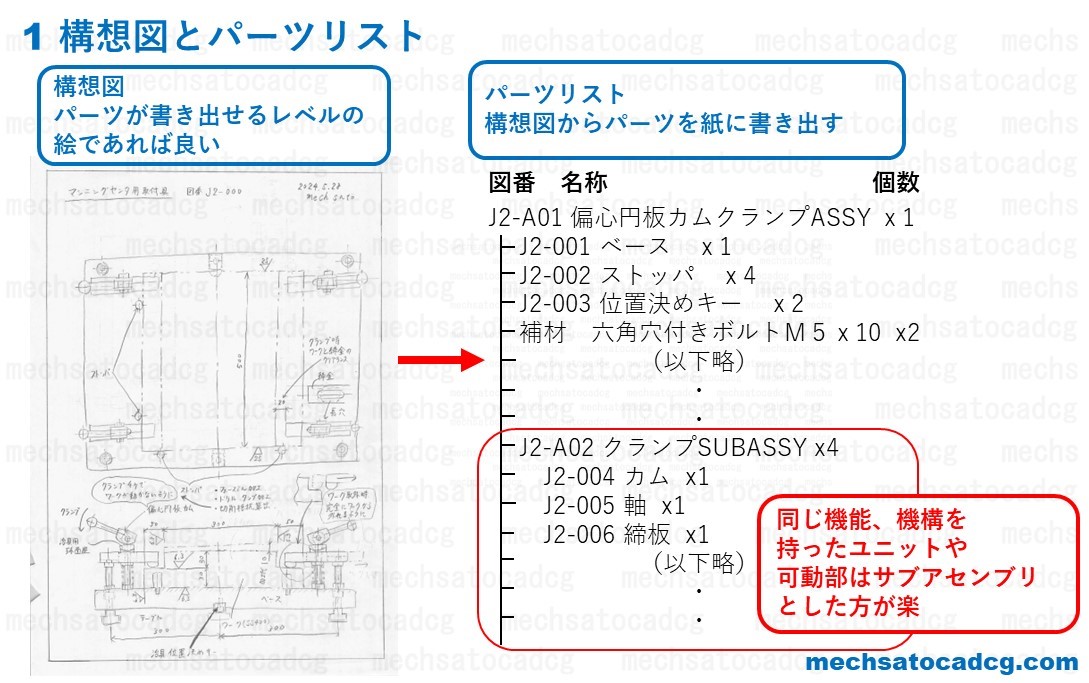
この段階で、図番が取れるなら、前もって取得してしまった方が、後々ファイルネームを変えずに済むと思います。
ただし、途中で部品が不要になった場合、欠番の扱いにならないように、別部品で穴埋めが出来るか、そのあたりも考慮しておかなければならないでしょう。
この辺りは前もって、設計部署内でルールを決めるか、上司や周りの人に相談して決めた方が安心かもしれません。
現在では、アセンブリ、パーツ、図面のファイルネームを、CADの機能や付属のソフトにより、互いのリンクが切れないように変更できるものもあるので、あまり神経質になる必要は無いと思います。
2.アセンブリ、パーツの作成
リストに従い、パーツの作成を行います。
この時作成するパーツモデルは、あくまで配置が出来るレベルのモデルで良く、フィーチャを1つ作成したもので構いません。
頭の中にある形状を、直ちに作り込むことはしません。
下図では、サブアセンブリ(クランプSUBASSY)に入るパーツのモデリングを、例として挙げています。
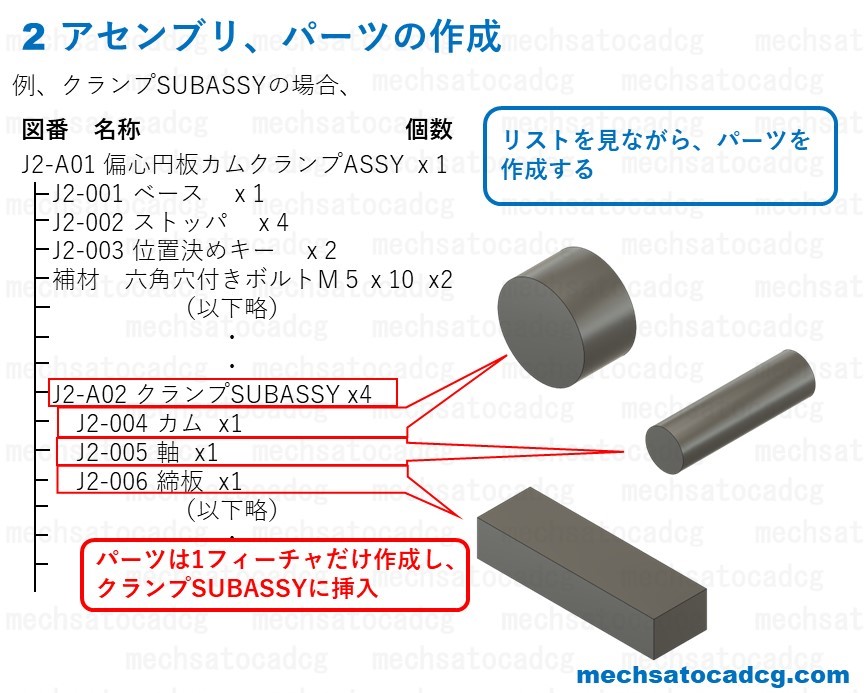
部品が軸であれば円筒状の、四角い板状の部品であれば立方体でパーツモデルを作成します。
この時の寸法は仮の寸法とし、後に強度計算等を行い、形状を決めていけば良いと思います。
3.パーツをアセンブリに挿入する
1フィーチャだけ作ったパーツを、サブアセンブリ上に挿入します。
この時点では、パーツの位置決めをする必要は無いです。
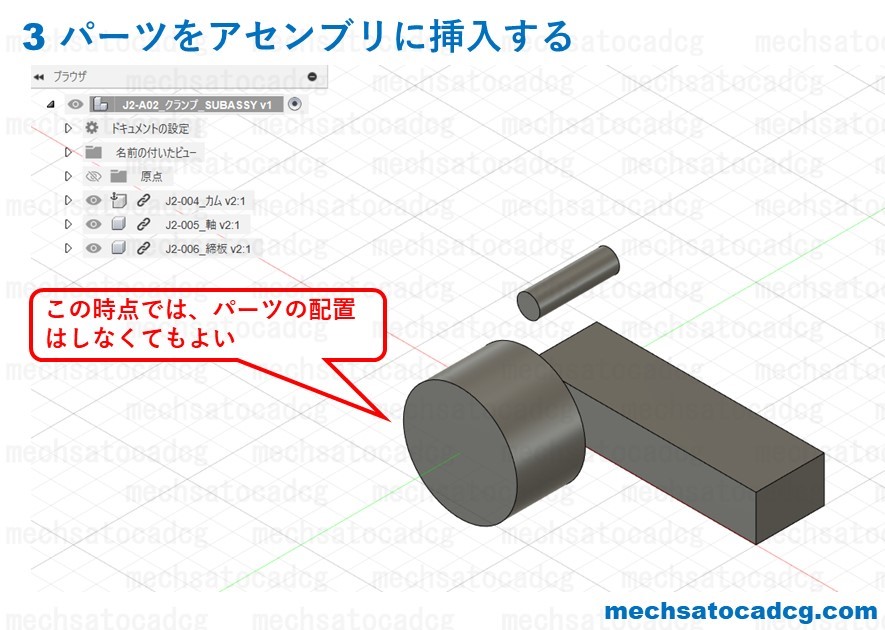
ここから先は、
4では、オーソドックスに、パーツ同士で合致をかけていく方法。
5では、アセンブリ上でパーツの配置を決める基準線をスケッチで描き、それに対しパーツを合致させていく方法。
以下、それぞれで説明します。
4.パーツ同士に合致をかける
方法の一つは、3で挿入したパーツモデルの主要部分……検討に必要となる部分から作成していき、その都度、合致をかけていく方法です。
3DCADのチュートリアルで、アセンブリモデルの作成方法を学習する際に教わるのが、この方法だと思います。
例えばリンク機構のリンク(節)なら、対偶素(リンクの接する部分)となる穴のみ作成し、他のリンク部品の穴と合致をかけてゆきます。
注意:最終的にピン等を作成し、この穴に差し込むことになりますが、ピンを介してリンクとリンクに合致をかけるのは、エラーの元になるので止めた方が良いでしょう。
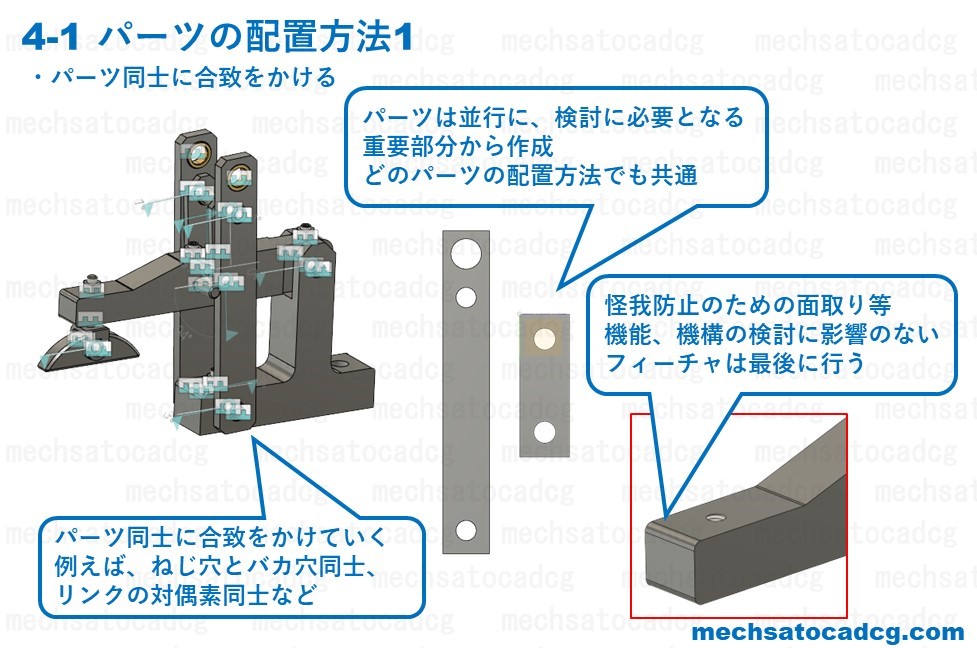
この時、面取りや部品固定の為のボルト類の挿入は後回しにし、とにかく設計する上で必要な部分の作り込みを優先して行い、意図した通りに機能を果たすかどうかを見ていきます。
パーツ同士に合致をかける方法のメリット
メリットとしては、
1、動きのあるものは、直接動かして検証が出来る。
動力を与える部分を、例えばリンクのクランクを揺動させたり、シリンダのピストンを押し込んだりして、動きの検証をすることが出来ます。
これは3DCADの大きな利点の一つですね。
2、部品の配置、合致をかけるのが楽
例えば、ねじ穴とバカ穴を合致をかけていく等、互いに固定しあう場所に合致をかけていけば良いので、合致のかけ方も分かりやすいです。

パーツ同士に合致をかける方法のデメリット
しかし、デメリットもあります。
1、重要度の高いパーツを編集したり削除すると、他のパーツの合致が外れたりエラーの原因となる
当たり前の話ですが、パーツ間に合致をかけているので、どちらかのパーツを削除すると合致が外れ、マウスでドラッグすると動いてしまいます。
また、穴位置を変更すると、穴同士で合致をかけていれば、エラーとなります。
2、合致のかけ直しやエラー修正に時間がかかる
一番ネックとなるのが、合致のかけ直しやエラー潰しに、時間がかかることです。
塵も積もれば山となるで、繰り返していくと膨大な時間を要します。
色んなパーツと合致の関係を持っていると、エラーの修正も容易では無くて、どうしても復旧できず、関連すると思われるパーツを全て削除して入れ直し、改めて合致をかけ直す事になるケースもあります。
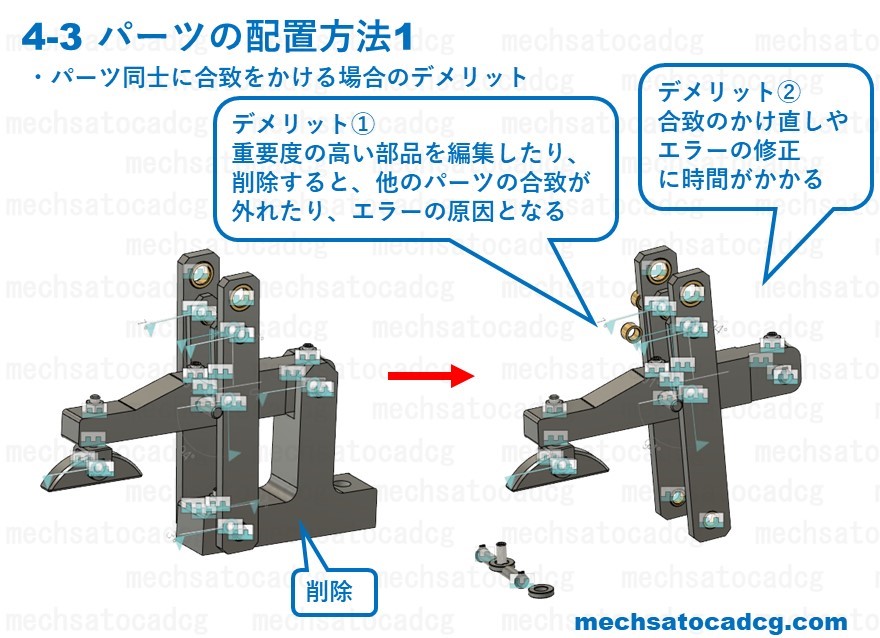
また、これは後々の話になりますが、他の人の作成したアセンブリだと、どこに合致をかけているか見極めたうえで修正をしていかなければならないので、かなり時間がかかります。
5.アセンブリにスケッチ作成し、そこに合致をかける
4で、ご説明した方法デメリットを解消する方法が、アセンブリモデル上のアイテム(スケッチ、基準面等)に対し合致をかけていく方法です。
ここでは、アセンブリにスケッチを作成し、そこに合致をかけていく方法をご説明いたします。
下図の通り、アセンブリモデルの中で、部品を配置できるように基準となる線を描いておきます。
部品の厚みや径などは、必要があれば描けば良いですが、基本は基準線のみで構成していきます。
例えば、リンクであれば、対偶素間の距離を表した一本線で十分です。
ただし、あらかじめ、寸法値を変更することで、機構が意図した通りに動くよう、スケッチに拘束や寸法を与える必要があります。
スケッチが出来たら、スケッチとパーツを合致させ、パーツの位置を決めてゆきます。
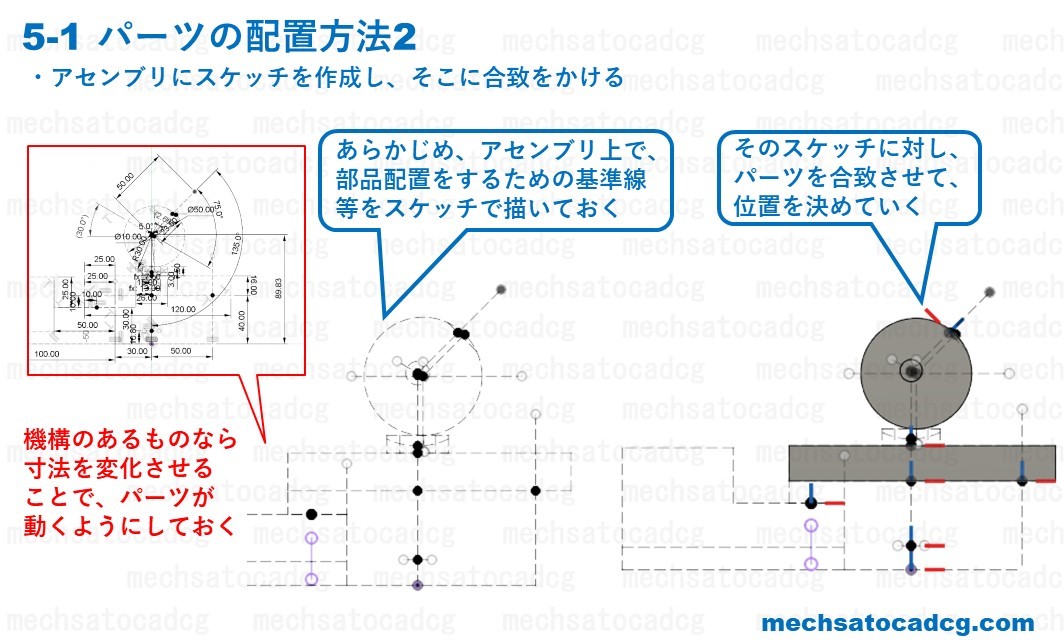
アセンブリにスケッチを作成し、そこに合致をかける場合のメリット
メリットとしては、
1、部品間に合致関係が生じないため、あるパーツを削除しても、そのパーツに関連したパーツの合致は外れない
スケッチに対し合致をかけているので、パーツを削除しても、そのパーツに取り付けられるパーツの合致は外れることはありません。
ただ、あらゆるパーツの配置をスケッチで用意するとなると、「このパーツの配置のためのスケッチはXZ平面、このパーツはXY平面」と切り替えてを描くのは大変ですから、締結用のボルトや位置決めピン等の補材に関しては、素直にパーツに対して合致をかけてしまっても、悪影響はまずないと思います。
あくまで主要なパーツのみで良いと思います。
2、部品間に合致が無いため、エラーも起きにくい
パーツの穴位置を変えたとしても、エラーの原因とはなりません。
(逆を言えば、穴位置がずれていることが分かり辛いとも言えますが……)
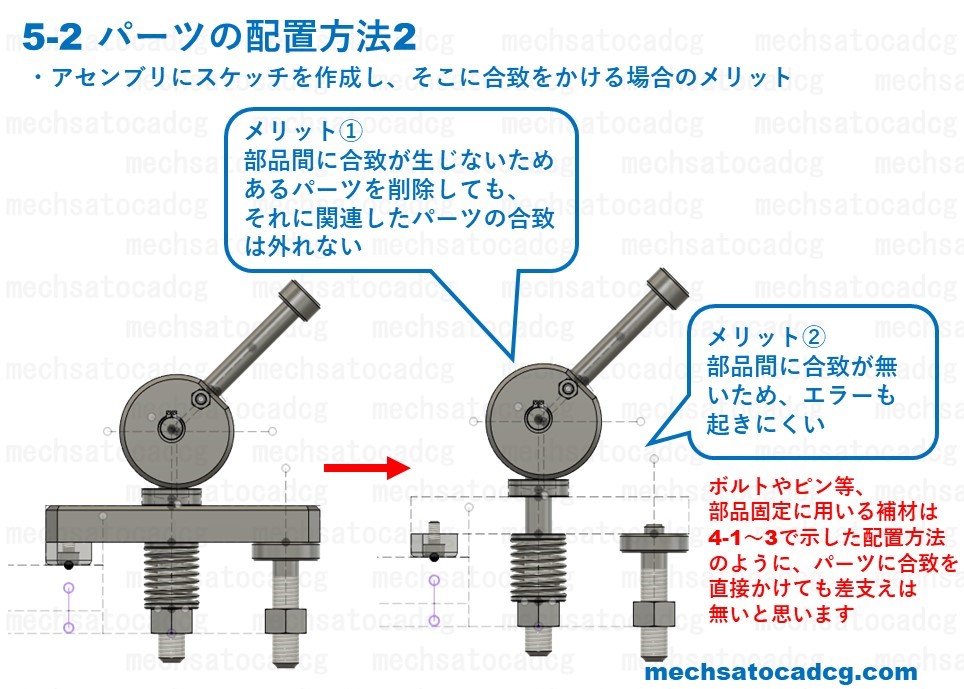
アセンブリにスケッチを作成し、そこに合致をかける場合のデメリット
4の手法の問題点を解決する方法が5の手法ですが、デメリットもあります。
1、直接パーツを動かして機構の検証などは出来ない
パーツの位置は、スケッチ上の基準線と寸法により制御される(決まる)ため、手で直接動かすことは出来ません。
動きの検証の際には、あくまで寸法変更により行います。
そのため、挙動や機構の連動の様子を確認することが出来ません。
2、ある程度、設計とスケッチ作成について熟練を要する
5-1の図に「機構を再現できるように」と記しましたが、ものによっては難しいです。
適切な拘束の解除、寸法の与え方をしていないと、スケッチ上での再現はなかなか難しいのです。
また、兎にも角にも、設計スキルがある程度無いと難しい部分です。
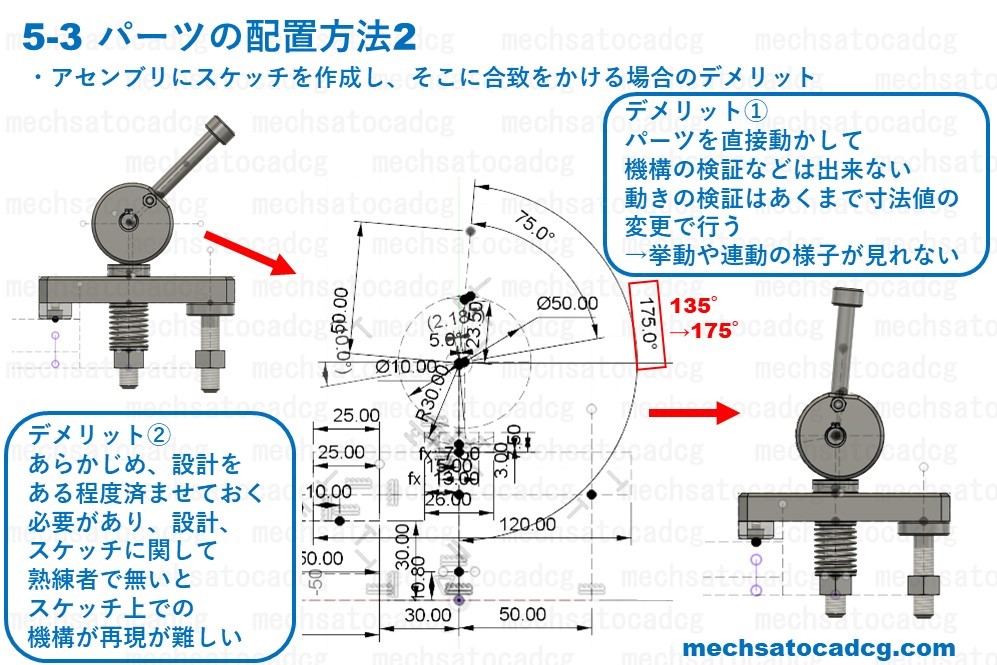
6.共通して行うべきこと
ある程度、アセンブリが形になってきたら、
1、強度計算をはじめとする技術計算を行う
構想図を描く段階で、出力や機構の速度、回転する部品の回転速度は仮計算を行い、「あたり」をつけておいた方が良いと思いますが、3D上での設計がある程度進み、重心位置、質量、慣性モーメントの高い精度で得られた情報を再度フィードバックし、動力が足りているか、要求された速度で駆動するか、計算を行う必要があります。
また、形状の厚みや径なども、力やモーメントのかかる場所は、強度計算を行い、問題が無いか確認しておきましょう。
2、干渉チェックを行う
ボルトやピン類等も合致も終わり、アセンブリ内の全てパーツの形状も面取り含めて完成した段階で、部品が食い込んでいないか干渉チェックを行う必要があります。
3DCADの利点の一つですが、頼りすぎると、設計者としての能力が衰えそうな気がしそうで、あまり好きではないのですが、必ずやるべきチェックだと思います。
7.まとめ
どちらも一長一短ありますが、設計時間の短縮という点では、5の手法が優れておりますが、私の経験上、4の手法で設計しているケースの方が多い気がします。
アセンブリに、スケッチ補助線や平面同士で距離を決めてパーツを配置していく会社は、今まで1社だけしかお目にかかっていません。
修正の手戻りの影響を考えた場合、小さいアセンブリモデルであれば4の手法が、大きなアセンブリモデルであれば5の手法が威力を発揮すると思います。
どちらにしろ、共通してやるべきは、
1、パーツのフィーチャは主要部分から優先して作成する
2、サブアセンブリ化できる部分は積極的にサブアセンブリにする
だと思います。
1は、いち早くパーツの主要な役割の部分を作り、検証、成立を確認することは、設計を進めるうえで優先される事項だからです。
これは2DCADや手描きの設計でも変わりません。
また、パーツの主要な機能は決まってしまえば変更されにくい部分ですから、なるべく他のフィーチャの変更による影響を与えたくないという理由もあります。
2は、アセンブリの一部をサブアセンブリ化することで、4の手法であれば、合致の関係の複雑さを解消することに繋がります。
これにより、エラーも少なくなりますし、サブアセンブリにすることで配置も容易となります。
ただ、どういった方法を取るべきかは、設計部署内で決めて統一するべきだとは思います。
3DCADの利点の一つである流用設計を考えれば、自分の作ったアセンブリやパーツモデルを他の設計者やCADオペレータが利用する可能性があることを忘れてはなりません。
以上、3DCADを使用した設計方法について、私の知る方法を解説しました。
少しでも、この記事が皆様の参考となり、お役に立てれば望外の喜びです。
【広告】
3D・CGモデリングのスキルを持った方々をお探しの方はこのテキストリンクから


コメント