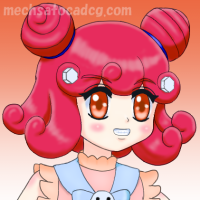
今回も前回に引き続き、機械設計の仕事についてね。
一か月近く待たされて、説明をせがんだ私も忘れていたけどさ……
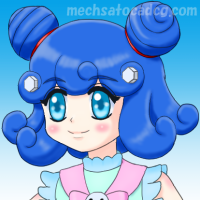
ま、まぁ、気を取り直して、前回の記事の冒頭でも示した、機械設計の仕事の流れを改めて見てみましょう。
機械設計の仕事の流れ(受注生産)
- 仕様打合せ…営業部が担当するが、設計者も同席を要請されることもある。
- 構想設計…仕様書を基に標準機に対し追加、変更される部分の構想図(ポンチ絵)を作成する。
- 詳細設計(計画図作成)…構想図を基に計画図を作成する。
- 承認図面作成…計画図を基に客先に確認してもらうための図面・承認図を作成、客先に提出。
- 詳細設計…計画図から部品図、組立図を作成する。
- 部品作成…製造部が担当。部品図を基に自社工場や加工工場に外注して部品を作成する。
- 組立…製造部が担当。製作された部品や購入部品を組立図通りに組立ていく。
- 検査…検査部が担当。組みあがった機械が仕様書通りのスペックを満たしているか検査する。
- 出荷…客先への機械の運搬し、据え付けと試運転を行う(製造部、サービスが担当)
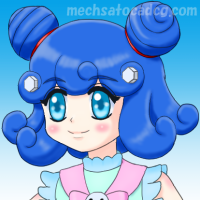
前回はお客さんとの仕様打合せ、仕様が成り立つように考えた機械の形状、機構を描き出す構想設計(構想図作成)、製作出来るよう構想図を具体化する詳細設計(計画図作成)、お客さんに承認を得るための図面、承認図作成までを説明したわよね。
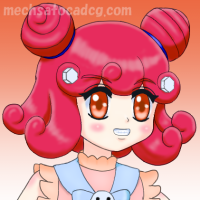
ええと、その続きは……
詳細設計(部品図、組立図作成)、部品製作、組立、検査、出荷、据え付け
……詳細設計から先は設計関係ないじゃない。
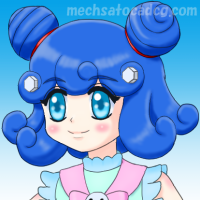
それが、そうでも無いのよ……
むしろ、設計が終わった後が大変かもしれない……
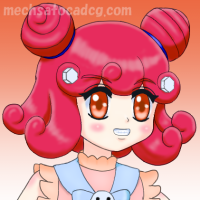
え…めかこ……
げんなりした顔して、どうしたの?
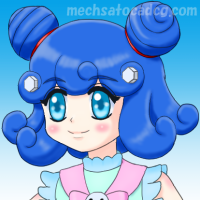
その理由は、この記事を読めば分かるわ。
と、いうことで、めかこちゃんの仰る通り、今回は書いていて胃の痛くなる話を多く……
というのは半分冗談ですが、場合によっては設計者の負担とストレスの多くなるのは間違いないです。
それと、設計が終わって製造に図面を出図したら、その設計の仕事はおしまい!という訳に、どうしてもいかないのが現実です。
では、詳細設計(部品図、組立図作成)から、ご説明いたします。
前回の記事はこちらです↓
【広告】
ものづくりのプロジェクト計画、設計、運用、構築ツールをお探しの方はこちら
3D・CGモデリングのスキルを持った方々をお探しの方はこのテキストリンクから


5.詳細設計(部品図、組立図作成)
部品図の作成について
商用図が承認されたら計画図を基に、まずは部品図を作図します。
手描きや2DCADで作業する場合、計画図から部品を抜き出して作図することを「バラシ」と呼びます。
自分で計画図を描いているのであれば、部品図の材質、表面粗さ、表面処理、熱処理の必要性については頭に入っていると思うので何の問題もなく図面を描き進めていくことができると思います。
しかし、他の設計者やCADオペレータに作図依頼をする場合には、打合せをして機械の仕様や動き、部品に関する情報を伝える必要があります。
また、似た設計や部品図があれば、それらを参考図として渡しておいた方が良いでしょう。
作図も円滑に進み、自分の検図も楽になります。
ただし、将来、機械設計者となる人には、社内規格から公差や表面処理、熱処理を判断できる場合は、規格から調べるように指示し、あまり教えすぎない方が良いと思います。
社内規格を調べる習慣を早いうちに身に着けておくと、構想図や計画図を描くときに楽になり、規格を見落とすことによる失敗も少なくなるでしょう。
ところで、部品図を描いていて最も迷うところはなんでしょうか?
多くの設計者やCADオペレータは「寸法の入れ方」と答えると思います。
寸法は部品の基準面や、加工方法を考えて入れていく必要があり、現場を知らない設計者やCADオペレーターは参考図が無いと、どう入れて良いのか分からなくなりがちです。
そこは先輩の設計者や上司に相談するしか無いのですが、時には現場で作業を見せてもらって、加工方法を知っておくことも必要なことです。
また、3DCADで部品図を描く場合、図の配置は楽ですが、手描きや2DCADで三面図を配置する場合、投影法をちゃんと知っている必要もあり難度も手間も上がります。
今後、この記事では3DCADで部品図が参照する3Dモデルを、パーツモデルと呼ぶことにします。
更に自動車業界を皮切りに三次元図面という部品を鳥瞰(斜め上から見下ろした図)で配置し、それに寸法指示や表面粗さ指示を入れた図面に切り替える動きも一部であるようです。
三面図がどうしても理解できないという方は実際にいて、そういう方でも図面が理解できるようにという配慮から始まったのでしょう。
どちらにしろ溶接記号や幾何公差等、製図記号の意味合いは勉強しておかなければなりません。
組立図の作成について
部品図を描き終えたら、次に組立図の作成を行います。
組立図は現場が組立時に使用するための図面ではありますが、設計者にとっても部品図から部品を抜き取り、組み立て順序通りに部品を組立てていけるかどうか検証するための図面だと、学校では教えています。
しかし、そもそも組立が出来るかどうかは計画図を描く段階で考えなければならないため、組立図=計画図という会社もあります。
時間に余裕のある会社なら良いですが、大抵設計者は忙しくて省ける作業は省きたいという合理的な判断からでしょう。
3DCADを使用している場合は最初から、前回記事で解説した2DCADにおける計画図、つまり3D検討モデルを更にユニットモデル単位に分解し、それを組立図の参照先とするのが一般的です。
ここではそのユニットモデルをアセンブリモデルと呼ぶことにします。
次に、組立図には組み立てられた機械の図示以外に、その組立図上で使用している部品を全て表に纏め、その表と図示した部品との紐づけを風船で行います。
それが無いと類似品や、特にボルト等はどこにどれを使っていいか分からないからです。
これはプラモデルを説明書無しで作れといっているようなもので、必ず組立図上に部品表と風船は必要となります。
次に組立図の寸法や図示すべき内容を下記にまとめました。
- 可動がある場合は最大、最小ストロークおよび回転時の状態を二点鎖線で示し、最小最大位置、可動域内で干渉が無いか明らかにする
- 組立が出来るか頭の中で想像し、CAD上で検証する。
- 機械の全高、全長、全幅を入れる
- 部品の取り付け位置が調整できる場合、その部品の定位置や部品同士のクリアランス寸法
- はめあい部の軸、穴径、取付穴の位置、これらは部品図で入れた寸法と一致しているか確認出来るように寸法の起点を部品図と合わせて入れる
1はその言葉通りで、まず入れ忘れるということは無いと思います。
2は組み立てができるか想像したり、実際に部品を考えている順序通りに組み立てられるかCAD上で部品を取り付けたり外したりして検証してみます。
この時は作業者や工具のことも忘れてはいけません。
例えば、ボルトをスパナで締め付けられるかどうか、スパナの図やモデルを組立図やアセンブリ上に持ってきて、最低60°は回せるか、手が入るか、作業者が無理な姿勢にならないか、作業者に危険が無いかを確認します。
3は言葉通りで組立後の最大寸法を入れておきます。
仕様に関わるというだけでなく、大きな機械の場合、工場で組立が可能かどうか、客先へトラックで出荷する際、分解の必要があるかの判断に必要となります。
4は取付部品がクランプ等で調整できる場合の部品の定位置や、機械上の基準からどの位置にあるべきかを寸法で入れておきます。
5は部品図と組立図が一致しているかどうか、検図に用いるためという意味合いが強いです。
3DCADで作業している場合、組立図の部品と部品図の部品に、まず食い違いは無いのですが、現場での寸法確認にも用いるため入れておくべきでしょう。
また3DCADであれば、分解図で表現もできるため、組立可否の判断もやりやすいです。
部品数が多い機械やユニットの場合、分解図は図面として作った方が良いでしょう。
ここまでは、どちらかというと2DCADをベースに組立図作成について書いてきました。
はっきり言って、組立図の作成は2DCADに比べて3DCADの方がはるかに楽です。
アセンブリモデルをきっちり作り、パーツモデル(部品図が参照する3Dモデル)のプロパティに図番や材質をしっかり入力出来て入れば、組立図上にある部品表にもそれが反映されますし、そもそもアセンブリモデルにあるパーツモデルが食い違っているということは、モデルデータの読み込みに問題が無ければありえないことです。
(むしろ、3DCADの運用ではデータの管理とルール作りがネックなのですが……)
部品表を作成する
部品図、組立図を描き終えたら、会社(設計部署)の定めたルールに従い部品表も作成します。
部品表(Bill Of Materials、通称BOM)は製作部品や購入品、ボルト等の補材を表にまとめたもので、製造部で部品の手配や購入のために必要とする書類です。
出図の際に部品図や組立図と一緒に配布するものです。
3DCADを使っている会社だと部品モデルのプロパティがしっかり入力できていれば、組立図上の部品表と同じものを部品表として出力できるようにしたり、PDM(※)に3Dデータを登録した際にで自動で作成できるようにしている会社もあると思います。
3DCADを使用していない、PDMを使っていない場合、部品表は組立図や部品図を見ながら表計算ソフトで作成する必要があり、不備があれば部品が製作されなかったり手配されない恐れがあります。
※ PDM
Product Data Managementの頭文字をとったもので、日本語では製品情報管理システムと言う。
社内にある図面データを集約し管理しているシステムのことを指す。
図面を描き終わったら自己検図を行う。
部品図、組立図を描き終えたら、すぐに上司や計画図を描いた設計者に持っていくのではなく、図面を全て印刷して自己検図を行います。
部品図と組立図を見比べて寸法に食い違いは無いか、寸法に抜けは無いか、同時に公差、表面粗度、溶接指示の抜けが無いかを見ていきます。
チェックした箇所には赤ボールペンでチェックを入れ、抜けや間違いがあれば書き入れたり訂正をします。
紙が勿体ないからパソコンの画面上でというのはやめておいた方が良いでしょう。
自分がどこをチェックしたか、していないかが判別できず不備を見落とす可能性が高くなります。
紙で自分が確認した箇所にチェック印を入れていくのが確実です。
現場で図面不備が発覚して、その対応を自分や生産技術、現場の人がするだけで、紙の数十枚の値段以上の損失が出るのは確実なのですから……
一通り自己検図を終えたら、モデルの修正、訂正部分の修正や寸法指示抜けの追記を行います。
修正した箇所にはチェック時に使ったペンと別の色のペンでチェックを入れると、修正や追記をしているか分かりやすいです。
モデル、図面の修正が終わったら再度印刷してもう一度、最初のチェック図面と新しく印刷した図面を見比べて、自分の指示通りモデルの修正や訂正、抜けの追加が出来ているか確認をします。
『紙が勿体ないなどと言っていられない』と先に書きましたが、この時、新たに印刷した図面の修正訂正箇所のチェックは、自分が分かる程度に鉛筆で小さくチェックを入れるようにするくらいでも良いでしょう。(印刷や図面の並び替え、図面自体の印刷漏れのチェックは時間もかかるので)
上司に提出する際には消しておきます。
ちなみに余談ですが、水色の色鉛筆はチェックに使っても印刷したときにチェックした印が、ほとんど出ないです。(強くチェックを入れると流石に移りますが……)
同じように、部品図、組立図と一緒に出図する必要がある部品表も、ここで抜けや不備が無いかチェックをします。
先に書いたように、部品表の不備も手配漏れに繋がったりバカに出来ないので組立図、部品図と見比べながら図面と同じようにチェックをします。
全てチェックが終わったら、上司、もしくは計画図を書いた設計者に検図をしてもらうため提出をします。
自分が完璧だと思っても、他人が見ると色んな抜けが見つかるものです。
「どんなに正確な人でも100作業をすれば1つは間違う」なんていう話もあります。
緊張はありますが、自分よりも経験豊富な技術者に見てもらい指摘をされることは、とても良い勉強にもなります。
こちらの記事で寸法を出来るだけ抜けないための防止策について説明しています。
よろしければ、こちらを参考にしてみてください。
既にある図面やモデルを使う、ちょっと変更して新図として使う場合の注意点
ところで、部品図や組立図、モデルの中には以前に設計製作し納入されたものをコピーして、必要箇所を変えて使うこともあるでしょう。
そのまま今回も使うという図面、モデルもあるかもしれません。
むしろ受注生産の場合そういう設計の方が多いと思います。
注意したいのが、既に一度作っているから問題無い、自分が設計変更する箇所にだけ注意すれば大丈夫だと思っていると痛い目に遭うことがあります。
普通に生産技術や現場から、その図面に関する問い合わせや不備の指摘が飛び込んでくることもあります。
部品製作や組立時に発覚した不具合や不備の対策を行い、図面の改訂を確実に優先的に行うように徹底している会社であれば、まず大丈夫だと思いますが、そうでない会社(設計部署)もあるわけです。
なので、特に図面改訂の対応が怪しい場合は、新規図面と同じように検図をした方が良いと思います。
上司の検図が終わったら出図をする
上司や設計者に検図をしてもらい、指摘された抜けや誤記、モデルの修正を終えて再度上司から完全にOKが貰えたら出図をします。
『出図』とは、図面を製造部や検査部に配布して、設計部から製造部に部品製作や購入依頼をすることです。(広く言えば、営業に承認図を提出するのも出図となります。)
部品表、図面を必要部数コピーして配布を行います。
出図も慣れるまでは結構大変で、時間のかかる作業です。
大きな会社では、出図を専門に行うグループがあるという会社もありますね。
自分たちで出図処理を行う際には、やはり部品表や図面のコピーし忘れや抜けがあると手配出来ないこともあるため細心の注意を払う必要があります。
ここまでが設計者の行うべき作業ですが、仕様打合せ(場合によってですが)、構想設計、詳細設計、承認図作成まで全て行う場合、その負担も責任も相当なものです。
人員が豊富であれば、部品図、組立図の作成は新人やCADオペレーターに、出図作業はアルバイトやパートの方を雇ってということも考えられますが、なかなかそういう動きにならないのが現実だと思います。
しかし、冒頭でもお話した通り、出図を終えたらその仕事は終わり……とはいかないものです。
それを以下の各工程でご説明します。
6.部品製作…設計には図面の問い合わせが来る
図面を配布された製造部では、部品図を製作する為の工程や使用する工作機械を考え、それに応じてNCプログラミングや場合によっては治具の設計製作を行います。
また、製作に必要な工作機械が自社に無い、もしくは製作するための余裕が無ければ外注に出して製作します。
図面に指定された材料や購入品の購入も製造部内にある購買担当部署で行います。
出図された図面について問い合わせが来る
図面寸法に抜けがあったり、材質や型式に誤記があったり、製作が出来ないような指示(例えば溶接で±0.1の精度を出せなど)が……とにかく図面に不備があると設計に問い合わせが来ることになります。
中には生産技術や現場の確認不足や知識不足が原因というケースも無くはありませんが……
出図した図面の問い合わせが、上司に連絡が来るか、設計した自分に直接連絡が来るかは会社によるところが大きいですが、とにかく無視はできません。(本来は検図した上司に連絡が行くのが、組織としては正しいと思います。)
納期を守るため、製作を進めていくために、今やっている作業を止めて対処する必要があります。
出図済みの図面にミスがあった場合、改訂という形で訂正追記を行い、再度出図をすることは設計部署としては何よりも優先しなくてはならないことだと思います。
少なくとも私はそう教わってきました。
前で述べた通り、そこで改訂を後回しにすると製造から指摘があったことを忘れ、図面は不備を残したままとなります。
不備のあった図面を次回も自分が使う場合なら、不備があったことを思い出すかもしれませんが、そうでない場合は別の設計者や製造部の人に多大なストレスと時間的損失を与えることになります。
無駄な時間=無駄な仕事=無駄な金ということですから、良いことは何一つ無いのです。
製造側でミスがあった場合も相談が来る
また、製造でミスがあった場合、どうにか出来ないか相談が来ることもあります。
例えば図面にある機械加工をする箇所の寸法が30mmとあったところを、2mmマイナスしてしまった場合、30mmの普通許容差は中級で±0.2ですから完全に不合格です。
しかし、製造しているものによりますが、特にはめあいや強度に関わらない場所で使用に問題が無ければ、そのまま進めて良いと判断し、進めるように指示することが多いと思います。
本来は不合格の部品を、合格品として使用することを特別採用、略して特採と言います。
とにかく大事なのは、こういう連絡が直接来た場合は、大小に関わらず必ず上司に連絡をして、どう対策するか情報を共有しておくべきです。
設計で何かあった場合、責任を問われるのは検図、承認をした上司なのですから、その上司が「知らない」ということはあってはならないからです。
特採の場合、図面の改訂は不要ですが、製造でミスをしたという記録は会社の定められたルールに従って取っておかなければなりません。
後々、万が一問題が起こった場合、その対策をするために必要な情報となります。
7.組立…部品製作時よりも設計に問い合わせが来る
部品の製作が終わる、もしくはある程度終わって、購入品が揃ってくると並行して組立が開始されます。
工程が下流に向かうほど、トラブルが起きると厄介なのですが、私の経験では部品製作の時よりも組立になってからの方が設計ミスの発覚が多いと感じます。
原因としては色々ありますが、ざっと思い出してみると、
- 組立図にある部品、購入品と部品図、購入品の寸法が合っていない
- 組立図の不備
- 部品表の不備、手配するべき部品が手配されていない
- 部品が図面通りに出来ていない
- 作業者が組立図通りに組立ていない
3~5は製造側の問題で、大抵、4と5はセットで発覚することが多いです。
次工程に流す前にちゃんと寸法確認しろという話ですが、納期がタイトな状況がずっと続いている会社では、そういう体制、習慣が無いことが多いです。
(そういう会社に限って、ISO9001(品質マネジメントシステム)を取得していたり……製造というより会社レベルで問題があるというべきでしょうか。)
現場や生産技術の恐い人から、すごい剣幕で設計に問題があると捲し立てられると、つい謝ってしまいそうになりますが、図面を一緒に確認して、製造側が間違いだと主張している部分を確認する必要があります。
余談になりますが、学校を卒業してから計測器具(ノギス、マイクロメータ)、工具を触っていない人は、思い出しておいた方がが良いでしょう。
最近はノギスもデジタルが多く普及するようになり、誰でも使えるようになりましたが昔ながらのノギスも使えるようにしておいた方が良いと思います。
問題は1~3です。
1は部品を流用している場合にありがちですが、組み合わせられる部品同士の穴位置にズレがあって組み付かないというのは、情けない話ですが意外と多いミスでしょう。
2は色々ありますが、風船が上がっていない、もしくは上げる部品を間違えている、図が小さくて見えない等、ミスを見つけ出して説明すれば、解決する軽微なトラブルです。
次にまずいのが、部品同士が干渉しているというケース。
あとは、板金製缶品など製作精度が悪い部品を使う場合に多いですが、組付けについて調整できるようにしていなかった、そもそも組立が出来ない等があります。
部品同士の干渉は強度に影響があるかどうか確認して、干渉部分をカットすれば良いので、大抵は短時間で解決します。
組付けの調整も削ったり、シム等を使って位置調整をすれば、短時間で済むことが多いです。
そもそも組立が出来なかったというのは、ケースにより解決の難易度が変わりますが、とにかく上司に相談して早々に解決案を出さなければなりません。
3で問題になるのは、部品が多かったり少なかったりです。
最悪なのが、納期のかかる部品や購入品が手配されていないケースです。
手配してすぐに入ってくるものは良いですが、製作や納入に時間がかかるものだとすると、納期に影響が出てしまいます。
高価な購入品や高価な材料の部品をいくつも手配してしまったなんていうのも、実際に騒ぎになっているのを見たこともあります。
購入品であれば返品することでお金は結構戻ってくるかもしれませんが、製作品の場合はどうにもなりません。
別の設計で使えれば良いですが、その機械だけに使う部品の場合、次に同じ機械が受注されるまで倉庫でホコリをかぶることになります。
これらを回避するには検図をチェックリストも使って、最低でもダブルチェックを行う以外ありません。
8.検査
検査では受注仕様書通り、社内の規格通りに機械が出来ているか検査を行います。
組立もなんとか終わり、無事出荷を待つだけだと思ったら、検査から問い合わせが来ることもあります。
試運転したら仕様や承認図にあるスペックを満たしていないだとか、安全性について検査基準を満たしていない……例えば回転部や、挟まれる恐れがある部分がカバーされていないなどがあります。
この辺りも業界や会社によって様々でしょう。
とにかく上司に報告して対策を行う以外ありません。
状況によっては詳細設計(計画図)、設計計算書に立ち返って確認、対策を行い出荷できるようにしなければなりません。
私の経験上、設計を都度注意深く進めていれば、検査の段階で設計に問い合わせが来ることはまず無いです。
製造がやらかしていたり、購入品の動作不良、電気設計側の問題というケースがほとんどで、その調査過程で不明点があれば問い合わせが来るというのがほとんどです。
9.出荷、据え付け
出荷および据え付けの段階で問い合わせを受けた経験は、付属品は客先に渡すのか、どこかに取り付けるのかとか、そのくらいでしょうか……
客先の機械設置場所に実は干渉物があったとか、準備してもらうユーティリティ(電線や配管)に問題があったとか、機械制御のプログラム(電気設計者が担当)に問題というのは、まれにありましたが、機械設計者が動く必要があるケースに遭遇したことは、今のところありません。
据え付けに関しても、あらかじめ取り交わしている承認図の内容から外れていなければ、まず問題は無いです。
この辺りは会社の風土もあるのでしょうけど、そもそも検査が承認図や仕様と出来上がった機械を照らし合わせ、試運転した上で出荷しても良いと許可を出している訳ですから、この段階で設計や製造の責任という形には出来ません。
検査がなんとか解決しようと動きます。
もちろん、上流工程の営業、設計、製造の責が全くない訳ではないですし、後々、各部署のお偉いさんが集まって責任の所在について喧嘩をすることになるでしょう。
まとめ
二回に渡って、CADをツールとして多く使うお仕事の一つ、機械設計(受注生産)の流れを解説してきました。
前回記事の最初にお断りをしましたが、これはあくまで私の経験に基づいたものであって業界、会社によっては異なるということをご理解下さい。
特に製造装置を想定しているので、航空機や自動車の開発設計とは流れが大きく異なります。
図面が出図された後に問題が発覚するのは異常事態なのですが、決して少なくないです。
そういった出図後の問い合わせが珍しい会社や体制作りがきちんと出来ている会社がうらやましいです。
経験のある方は分かると思いますが、別の仕事に取り掛かっている中で前にやった仕事の対応をしなくてはならないストレスは、尋常では無いものがあります。
それを防ぐには、
- 仕様に少しでも不明点があれば、放っておかずに上司や営業に問い合わせる。
- ゆとりを持って作業し、チェックリストがあるのならば手を抜かずにチェックをする。
- 検図も出来れば二回行う…特に余裕があるなら日を置いて検図をすると、自分が描いた図面でも先入観が薄れて新鮮な目で検図をすることが出来ます。
自分が良く起こすミスがあれば、ミスをしないようにするにはどうすればよいか、考えて対策をしておく必要があると思います。
とにかく、上流で不安点やミスは無くすことが重要です。
……なんて偉そうなことを書きましたが、私もやらかすときはやらかしますけどね。
話は少し変わりますが、製造業での人手不足や技能継承はずっと課題となっています。
はっきり言って、教育に関しては新人、受け入れ側も余裕が無くなって、何年経っても芽が出ないなんてケースを多く見てきました。
このブログの機械設計やCADの記事は、設計業務を始めた方や教育する人の苦労が和らげばいいなという気持ちで書いております。
私もまだまだな部分もあるのでスキルアップをしながら、このブログの訪問者の方にとって少しでもお役に立つようなブログを目指していきたいと思っています。
【広告】
3D・CGモデリングのスキルを持った方々をお探しの方はこのテキストリンクから


コメント